Experience Matters
You can filter your search by typing in an employer name, or selecting a major. This is a great way to see what possibilities are out there!
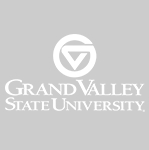
Genesis Seating Co-op Experience
Leif
Major: Mechanical Engineering
My main task at Genesis Seating was to design and create assembly fixtures and part carts. I would be given a problem that the floor workers are experiencing and would have to come up with a way to solve that problem. Most of this just entailed designing a fixture that would hold the part being worked on in a certain orientation. I was also task with doing time studies. This is a way for Genesis Seating to make sure what they quoted a company for labor cost was correct. I would simply watch the work assemble a chair and record the time it took he/her.

First Co-op: Quality Control
Kyle
Major: Mechanical Engineering
I performed calibrations on tooling as well as measuring equipment. I helped convert from an old tool maintenance database to a new more professional database and wrote all new work instructions on how to calibrate each set of tools that was stored in their ISO standard. I also helped do a return on investment project to help determine if a new program would be worth the investment.
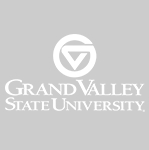
Mechanical Engineer Co-op
Jared
Major: Mechanical Engineering
AutoCAD, ELMII, and SMM were all software (some developed by Dematic) used to create a layout for a customer, order it, track it to the site, and observe it being built.
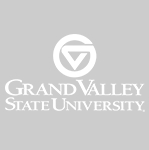
Real World Engineering
Caleb
Major: Mechanical Engineering
While my time at this company, I was able to work first hand on the automated equipment. I was able to troubleshoot problems, ensure proper assembly of the parts and overall prove out of the machines. I was also able to install, power up, and service the machines that this company put into factories.
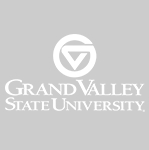
JR Quoting Intern
Ben
Major: Mechanical Engineering
I quoted material handling cells that would use robots to move parts around and torque bolts to a certain specification. I quoted mold tending cells with robots that would retrieve molded plastic parts from and injection mold machine. I quoted assembly stations that would verify the operator assembled a part correctly.
JR has a vast customer base and there were very few quotes that were alike.

Co-op II
Stephen
Major: Mechanical Engineering
I worked as a CAE analyst. I did FEA analyses of the crash tests we perform in the tech center. When we crash a vehicle into a wall, we simulate the same crash in the computer and compare results. We heavily rely on FEA in the design process to improve our designs. My main projects were simulating two manufacturing processes: (i) stretch-bending aluminum extruded beams and (ii) sweeping roll formed steel beams. Both of these simulations were created to evaluate manufacturing feasibility.
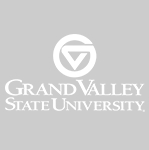
Co-op II with Dematic
Jared
Major: Mechanical Engineering
For each project conveyor is quoted and then sent to the application engineering department for refinement and editing based on what the customer orders. After the plan and elevation drawings for the logistics system are completed, the conveyor is ordered using an in house software package called ELM II (Equipment List Management). After the conveyor is ordered and installed on site the engineers visit the site to test, commission and hand the site over to the customer.
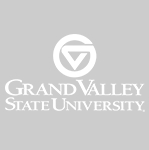
Ravenna Ductile Iron
Eric
Major: Mechanical Engineering
Clean and inspect patterns that have recently been in production for any wear, breaks, or broken parts.
Many projects that I worked on included completed redesign of pattern layouts for new and old tools. Pro/E Creo Parametric 2.0 was used to place castings on a plate that would be optimal for gating that were calculated.
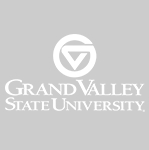
Summer Co-op I
Marshall
Major: Mechanical Engineering
Technical documents such as mill operator's manuals were written. Process studies on roll forming mills were written, executed, and documented regarding the weld bridge, jack stand, and the sweep unit.
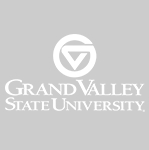
Trane Summer 14
Albert
Major: Mechanical Engineering
I mainly learned everything that goes into a modern day HVAC system. I also was taught psychometrics and common air flow calculations.
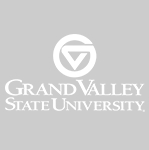
Gentex Glass Bending - First Round
Andrew
Major: Mechanical Engineering
I worked in the Glass Bending group, and to begin I, just like everyone who comes through and works at Gentex, had to learn the product. I spent two weeks on line, taking glass from flat lites, cut to basic shape, bent, cured, and inspected before moving the glass on to be coated. As all of the engineers at Gentex begin as Production Support Engineers, it's important to understand the whole process per area so that any improvements are made with a good knowledge base. I began my projects with basic line improvement items, building a guarding door, a chute for rejected glass, lots of work with 80/20 aluminum. I then began more intensive projects, like a glass inspection improvement project, where I was teamed with another intern to find a better, more efficient method to inspect glass of a certain coating. We were given free reign of our ideas and funds, and were able to come up with something that in the end may save the company quite a bit. I also was given the task of improving materials used to handle hot glass on the end of vacuum cups, doing research on each, price-justifications, and working with outside vendors to obtain samples and eventually order for production. Throughout the semester I gained more and more autonomy, taking over some continuous projects such as leveling benders, and tracking press counts, and all of the data manipulation involved

Gentex first co-op
Derek
Major: Mechanical Engineering
In my role at Gentex, I was able to work on many different projects and in several settings. Some of my projects were designed work and solid modeling. Other times, I did more hands on building of projects. As the co-op continued, I began to develop more of a leadership role, and was given the freedom and responsibility to help with some issues on the production line. While working in the process engineering department, many of my projects were related in nature. I designed and modified flow racking which presented material to the operators in ways that would speed up production and not damage parts. Similarly, I also designed fixture storage within the production lines that would allow for faster change-over times, cleaner lines, and less damage to fixtures. Many of my projects also focused on modifications to machines and revisions to their documentation which would fix a problem seen within production.
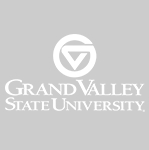
Setting up my Future
Tyler
Major: Mechanical Engineering
The project that I was assigned as part of my co-op experience at Flextronics was to improve the gauge management of plant I was stationed at. This included figuring out the standard procedure for introducing new gauges into the plant, writing verification and calibration procedures for the gauges, and evaluating the possibility of integrating new technologies to improve the efficiency of gauge management.
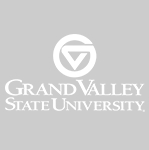
First Term Co-op at Bissell
Nicholas
Major: Mechanical Engineering
At BISSELL, I completed a lot of real world engineering projects. Though it would be impossible to name them all, I will name a few. I spent much of my first semester designing a separation system for a deep cleaner. I worked with an engineer on the project and learned a lot on the movement of an air and water combination. I later worked with another engineer on developing a weight projection calculator to be used in order to prevent problems during the prototyping stage of a project. There was also time spent learning many machines in the design lab as well as a lot of the equipment in the test lab that were new to me.
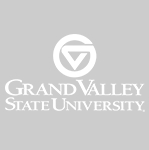
Co-op 1
Michael
Major: Mechanical Engineering
I did a lot of testing and benchmarking for many different inside and outside mirrors as well as designed small parts for prototypes.

Trans-Matic Co-op
Reid
Major: Mechanical Engineering
Engineering print updates, tooling design, press accessory design and implementation, 3D modeling, brainstorming, and tooling pricing estimation.

ME Co-op at BISSELL: Rotation #3
Carlos
Major: Mechanical Engineering
I have done many smaller tasks throughout the semester which consisted of performing tests and organizing data for reports, but I have worked on two large projects that have spanned the entire semester; liftoff/pivot project and MTU fixture project.
In the liftoff/pivot project I was presented with a set of problems and issues with a new product platform and was asked to design/develop a solution to those issues. Concept generation, design calculations, CAD work, physical prototyping, and a final design presentation were all stages of this project.
The MTU fixture project consisted of reprogramming a motor for a test fixture. This required calculations to determine a new gearhead and motor to purchase and further calculations to effectively code the programmable motor. Along with this, I was also tasked with training certain individuals on the device and provided documentation for future users of the fixture.
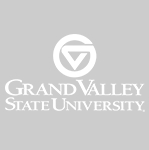
Process Engineering Internship
Andrew
Major: Mechanical Engineering
I did a lot different design projects over the summer. I designed several nests that are used to hold parts while they are tested for different things such as how much torque it takes to move the mirror as well as testing the leak rate to ensure the parts are sealed. I also designed an adapter which will be used to leak test some of the parts in a more convenient way than they currently are tested and in a way that is the same as the rest of the parts that we make.
I also designed a vacuum system that takes the backing that is peeled off of a glass element and sucks it away into a trash can. The backing is very statically charged after it is peeled off so it was causing a mess and sticking to everything so this will solve that problem
I also designed an enclosure to go around a machine to make it safe for someone to operate. This was a very good experience because it was very open-ended and allowed me to be creative with the design.
There are many other things that I designed and built over the summer that were a great experience and I learned a lot from them.
All opinions, conclusions or recommendations expressed are those of the author(s) and do not necessarily reflect the views of GVSU.