Experience Matters
You can filter your search by typing in an employer name, or selecting a major. This is a great way to see what possibilities are out there!
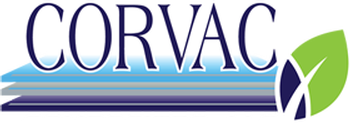
Engineering
Conlin
Major: Mechanical Engineering
1) Updated a Parts Reference Manual for Program managers
2) Created standard work, job breakdown sheets, and corrective action sheets
3) Capability study of Machines
4) Worked with IT to create a Design Request form online for the program managers to submit to designers
5) Worked with automation engineer on programming and modifying machines.
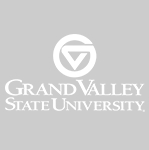
New Industries, New Experiences
Matthew
Major: Mechanical Engineering
I worked to design, build, and test a safety device to be used for repairing automotive batteries for new lithium ion batteries.
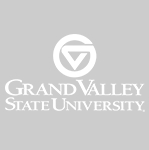
MotorGuide
John
Major: Mechanical Engineering
Built up a lot of test samples for product development. Mainly worked in the development process for two of the trolling motors that are launching. Helped perform tests for the motors to validate the product. My main project was to make a service tool for one of the motors that could be distributed to about 300 different service centers across the US
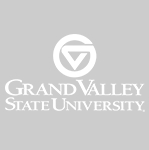
Engineering Co-Op Program
Artur
Major: Mechanical Engineering
I worked on the 3-D modeling of the patterns that make the molds that make the castings.
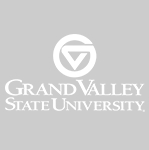
Dematic Summer Co-Op I
Jillian
Major: Mechanical Engineering
While at Dematic, I was assigned to a project that was in its final stages. It was a huge sort center and one of the first of its kind. The team didn't have a lot of information to reference back to in order to see how a site like this was done in the past. I was able to edit drawings where needed, order parts to get shipped to site, print blue prints of all sections of our conveyor and go to the site to help installation and start-up run smoothly.
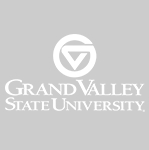
Fall 13' Co-op Experience
Eric
Major: Mechanical Engineering
Working as an engineering intern I started back in the lab where we test the physicals, chemistry, coating weight, and hardness of the material. After working in the lab for several months learning the system and type of material I was promoted to a material analysis job where I reviewed the results tested by the labs to determine whether or not the material would work for customer orders. I have also worked in the purchasing department as well as quality support. Mill Steel has allowed me to get a great feel how the business works.
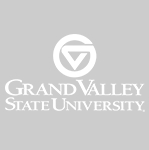
EGR Co-op Third Rotation
Reid
Major: Mechanical Engineering
This semester I worked primarily in the mechanical design group. I had numerous projects where I was the only engineer assigned to the project. On the majority of my projects I was supplied with data from the customer and was required to fully design a machine that would meet the customer's requirements.
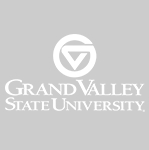
Amazing Hands-On Padnos Co-op
Jason
Major: Mechanical Engineering
This semester we have been installing a new non ferrous metal mining plant. I have been assigned
design work, drawing/detailing, overseeing of fabrication, surveying, product sampling, and experiment design/implementation; among a variety of other tasks.
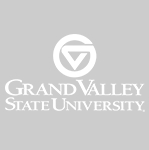
Real Experience
Tyler
Major: Mechanical Engineering
I worked as a student engineer at Midway. My job was to prepare operational manuals for all the equipment that was designed and built. This required me to have extensive knowledge in the mechanical function of all equipment I was assigned to. I also had to review equipment models/drawings to ensure no parts would interfere with one another and that proper GD&T was practiced.

Third Times a Charm
Nick
Major: Mechanical Engineering
Analyse and design parts used on hydraulic cylinders
Designed and updated floor plan layout of building
Organized the return department to track ongoing quality issues
Designed tooling to ensure quality of seals during assembly
Investigate floor changes throughout the manufacturing process
Helped standardize parts for quicker lead times
Devised an engineering test plans for performance testing of inserts
Organized tooling and machine lists to optimize efficiency
Headed machine repair software to schedule machine maintenance
Designed a torque bench for assembling or dis-assembling large cylinders

Engineering Co-op
Conlin
Major: Mechanical Engineering
Daily Tasks:
1) Walk-around to ensure production being maintained
a. Making sure processes are being followed (Standard Work)
b. Watch for waste in processes
c. Solve issues identified by Members
d. Make sure areas are 5S compliant
2) Quality Control
a. Ensure parts are being hung properly, i.e. Correct Rack and Orientation
b. Ensure parts being unloaded onto correct racks
3) Performance
a. Ensure line density is to standard per part and rack
b. Check to make sure members are being flexed properly
Also worked on Projects for paint line, component assembly, and the warehouse

1st Co-op Semester
Matt
Major: Mechanical Engineering
As an intern with previous knowledge of Pro Engineer (Creo), I was able to fill a need in the outside mirrors division as an FEA resource. I performed both static load and force frequency response analyses on many mirror programs. I then was also able to take my results and apply changes to the model in order to make recommendations as to how to make improvements.
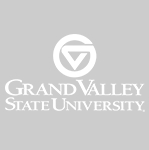
Automation Sensation
Andrew
Major: Mechanical Engineering
I worked on projects with more experienced engineers, completing smaller parts of their larger projects. I would do ProE CAD modeling and drafting frequently. I would also work in the quoting office, estimating costs and writing proposals for new work that the sales team would bring in.

Co-op at BISSELL
Thaddeus
Major: Mechanical Engineering
I ran tests on dry time and cleaning score of carpets, designed and prototyped concepts for a side brush and foaming nozzle, and gathered data from the company database and the internet.

Designing at JR Automation
Lauren
Major: Mechanical Engineering
During this co-op, I was in the mechanical engineering department at JR Automation. One of my big projects was designing a robotic cell that assembled a chair frame. All of the modeling was done in Pro/E. I took it all the way from kick-off to release and went through the design process of concepting, modeling, getting approval, detailing, checking, and releasing the project. I also worked on modifying and adding on to previously designed projects.
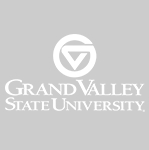
First Time Around
Nick
Major: Mechanical Engineering
I had three major projects during the semester along with many other small ones. My first project was to fix the steel plug problem. Some customers request steel plugs which cost about $0.75 per plug and some cylinders require up to four. All other customers get plastic cap plugs which are fractions of a penny. My job was to find the jobs that required steel plugs and add them to the bill of material so the inventory was correct and our costs were accurate.
My next job was to try and standardize the tangs. First I had to clean up the descriptions and dimensions so the parts could be easily searched. The overall goal was to find parts that are used repeatedly and have high usage. Out of about 370 tangs we have, about 40 of them consisted of 70% of the tangs used in the last year. By making these parts standard we can order larger amounts and save money making less custom parts. Another benefit was to have a list of parts that can be made from a standard part which will add to the total usage of the standard part.
My final project of the semester was to design a torque multiplier or a "Nut Buster". Basically we will be having some large cylinders come through the shop and we needed a device that will be able to torque the nut on and off. By bench-marking I was able to find a design another company had used and was able to make a similar design, why reinvent the wheel was my though. So by using two cylinder and a ratcheting system we can create about 26,000 foot pounds of torque. This system is mounted to a 14 foot long table with adjustable v-block rests and a brace to hold the other end of the cylinder. Very fun project to end the semester and it was nice being trusted with designing a machine we have never made before.
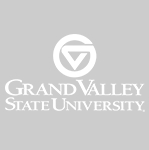
Gentex Summer 201
Dan
Major: Mechanical Engineering
Worked on an assembly line for the first week to become familiar with processes. Shadowed a Production Support Engineer to become familiar with troubleshooting the automation equipment. Constructed automation guarding using 8020 extruded aluminum. Completed multiple design projects using SolidWorks and had the parts fabricated by submitting tech drawings to the tooling department. A number of projects also required significant research for proper materials to use.
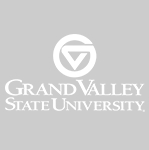
Summer 2012 Mill Steel Co-op
Ryan
Major: Mechanical Engineering
I tested steel samples in the lab for chemical and physical properties, reviewed these test results to verify accurate properties, and worked with business representatives to fit individual steel coils to matching customer orders.
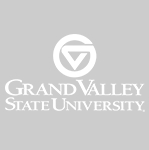
Everything is bigger at Padnos
Nathan
Major: Mechanical Engineering
I did everything from detailing a small handle on a hydraulic line to redesigning a conveyor belt, which included measuring the belt and the guards on the belt, taking the information and processing it in SolidWorks, redesigning the belt, and then sending the work down to the machine shop and finally seeing it taken out as a finished product. I was kept pretty busy throughout the semester with a variety of projects resulting in a variety of experiences for me.
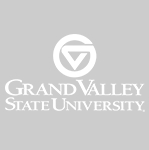
My Internship at JR Automation
Colin
Major: Mechanical Engineering
I was a concept and cost engineer, or quoter. I completed quotes for machinery. My job started by receiving the request for quotation from our salesman, doing the necessary research, concepting, and preliminary design for the quote, and ended by getting approval from the necessary personnel and having the quote sent to the customer.
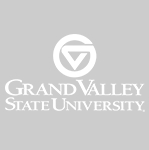
Trane Internship
Luke
Major: Mechanical Engineering
I worked on the graphical user interface between for the HVAC equipment and modified control drawings for the instillation of HVAC controlling equipment.

EGR290 Co-Op
Artur
Major: Mechanical Engineering
Working alongside the Process Engineer I worked on designing and improving patterns. These patterns are attached to a giant machine called the DISAMATIC(video) that compresses and makes impressions in a special type of sand. Molten metal is poured into these molds. After cooling the solid metal part comes out at the other end.
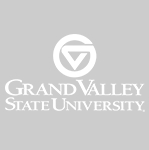
Envirotronics gives practical experience!
Jeffrey
Major: Mechanical Engineering
I started out by going through a lot of the old prints and updating scrap costs. By doing so I began to understand how they organized their prints. I did some cataloging of parts which helped me to understand how important correctly labeling parts is. I also did some excel documents that dealt specifically with engineering calculations. I did some designing of simple parts that were to be used on projects using AutoCAD and Pro E. Using those same programs I redesigned a few chambers so that they could be sent out for customer approval (mostly editing the drawings and parts, not actual design work). I also did a lot of dimensioning/editing of drawings for other engineers.

A Grand Experience, at Johnson Controls
Omar
Major: Electrical Engineering
I learned the specifications for two products that are being released in a future model of a major car brand, and applied that to the testing that was conducted on the software. I automated the testing on certain features to save time on current/future testing on this product and future products similar to it.
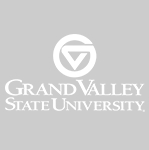
Mill Rebuild
Nathan
Major: Electrical Engineering
Provided instructions on how to install welding gas regulators on several welding cells. Also provided support on the major overhaul of one of their many rolling mill lines.
All opinions, conclusions or recommendations expressed are those of the author(s) and do not necessarily reflect the views of GVSU.