Experience Matters
You can filter your search by typing in an employer name, or selecting a major. This is a great way to see what possibilities are out there!
Cleanroom Chronicles III
Willy
Major: Electrical Engineering
I was assigned a couple of tasks as the semester went on. The main task was to design and manufacture (using in-house machines) a structural extension to an automated arm in order to fit the constraints of the environment it is operated in: a wet bench used in the College of Engineering's cleanroom.

Embedded Systems Engineering Co-Op II
Kurtis
Major: Electrical Engineering
I was assigned to the custom logic team for this particular semester. Thus, I became familiar with writing professional VHDL code and I wrote VHDL modules for commonly used modules intended to be used for future SoC designs. Furthermore, I completed simulations to ensure VHDL module behavioral functionality.
I also wrote Python and C code for an internally developed custom logic software tool that enabled engineers to conveniently compile VHDL cores.
Lastly, I worked on integrating an Aptina camera board with a daughter card and a Stratix IV FPGA. The daughter card and the camera module weren't designed to directly interface with one another; thus, careful board bring-up and testing procedures were performed. PCB modifications were performed as well.
I also helped configure the video processing SOPC modules. Moreover, I wrote C code for the embedded NIOSII on the Stratix IV in order to configure the SOPC video modules. SignalTap was used to obtain empirical samples of the internal signals within the video pipeline for debugging purposes.

The JCI Experience
Timothy
Major: Electrical Engineering
Test development in support of Homelink and related testing procedures.

EE - Controls
Ben
Major: Electrical Engineering
*Designed electrical, pneumatic and hydraulic prints for machines.
*Standard electrical codes and practices
*Wrote machine PLC logic and programmed HMI screens
*Some robot programming
*Camera/Vision work (part defect/presence)
*In general figured out how hardware worked and how to use it.

Industrial Eye Opener
Nathan
Major: Electrical Engineering
The picture attached is a picture of the biggest
project i had this semester. It controlled a
pneumatic cylinder that cycled in and out on a predetermined duty cycle and kept track of the # of
cycles. It was implemented to test the durability of
a new wire wheel system to de-burr the sharp parts.
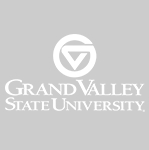
Project Coordinator
Sam
Major: Electrical Engineering
Coordinated an industrial automation upgrade project, to include researching available options, coordinating vendor meetings, creating and submitting request for quote (RFQ) documents, evaluating potential solutions. Future work to be performed includes negotiating terms of purchase, generating statement of work (SOW) documents, installing and testing hardware and software, developing a high-level user interface, and providing long-term support for the finished product.
Purchased components for, assembled, programmed and installed a large-format ambient temperature and humidity monitoring system for a controlled environment testing laboratory.

Future Gadgets
Omar
Major: Electrical Engineering
I worked on a product that will be released in a future model car, that I cannot disclose.
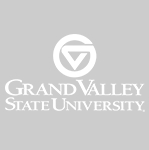
Third Engineering Co-op at Johnson Controls
Xu
Major: Electrical Engineering
I worked on software detail design documentation for software architecture design. I also participated in updating a database and project management documentation maintenance activities.

DornerWorks EE Internship Rotation 1
Josh
Major: Electrical Engineering
I was placed as a Custom Logic Intern at day one. I had to quickly pick up the basics of Python and C++, as well as become loosely proficient in VHDL, 3 languages of which I'd never done any work in. Some of the main tasks I've completed were writing test cases for a Single Port RAM, and adapting a VHDL Pseudo-Random Number Generator to our libraries and adding functionality to it.
Welding Robot
Corey
Major: Electrical Engineering
I was assigned to the headrest launch division where we assemble machines that bend and put notches in the metal headrest tubes. My major task for the summer was to help assemble, program the PLC and program the HMI for a Weld Cell that used a robot arm to weld up to six different stations around a 7 sided structure.
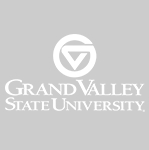
Inrad Inc Co-op
Patrick
Major: Product Design and Manufacturing Engineering
I was responsible for monthly maintenance procedures, designing and implementing fixtures, writing, quality assurance and performing testing protocols and other day to day operations as necessary.
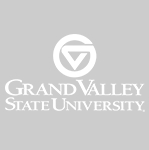
First Co-op Semester at Faurecia
Amanda
Major: Product Design and Manufacturing Engineering
While working at Faurecia xWorks in Holland I had the opportunity of working on components of major projects that were already in-progress. I also performed research for new projects and interests. During my semester I was also asked to execute tests of projects that were near completions.

Working at GHSP has Been a Great Experience.
Hayden
Major: Product Design and Manufacturing Engineering
This semester I was tasked with creating a system of visual scheduling for our electronics department. What my boss wanted me to create was a pull system closest to our customer. Currently, our planner schedules the week's products at the first work centers in the electronics area, the SMT's. The products are then arbitrarily forced through the other work centers based on what needs to be finished first. The electronics coordinators walk through the floor every morning and count the parts in progress to determine what we have and what still needs to be done. This leads to certain products sitting and waiting for long periods of time, parts getting misplaced, and inaccurate inventory counts. The pull system I have designed will utilize Kanban cards to move product through the various work centers. I calculated how often we can build the necessary products through the necessary work centers to meet our demand and based a supermarket for our finished goods off this interval. These supermarkets are designed to hold enough products to meet the average daily demand, to supply demand while the supermarkets are being replenished, and then a two day safety buffer. This buffer will slowly decrease as the system improves and there is less error. There is a similar supermarket setup inside the electronics department for the WIP. This is where the product is waiting to be used at some work center. There are two sets of cards that move with the products. One card follows the trays of WIP around the department, tracking its progress. The other set of cards follows the totes of finished goods from the last work center to the finished goods area. The finished goods cards are stored on a board denoting three separate areas. These areas are coded green, yellow, and red. While all of the slots are filled, the finished goods area for that product line is full. Every morning, a coordinator goes out and pulls the number of cards that meet that day's shipments and places them on the previous work centers build board. This signals them to start building certain products from their WIP area. As more cards are removed for shipments, the lower the supermarket gets, and the more into the red the finished goods cards go. This provides a visual way to see how much product is in the supermarket at any given time. As the work station consumes trays of WIP, they remove the WIP cards and place them onto another card board. This WIP card board has the same color coded slots. When a certain level is triggered, the cards are removed and placed at the SMT build board. This triggers the SMT's to start more products to replenish the WIP. The coordinators distribute the cards from this build board to the lines that are ready, or near ready to changeover to a new product. So far my system is only operating for three products from one work center. My boss wanted me to focus and start with these part numbers since they are some of the largest demanded products from our electronics department. There are a few more tweaks to this initial experiment that need to be made before it is rolled out to more work centers. I will continue to work on this part time throughout the summer.
Read More About Working at GHSP has Been a Great Experience.
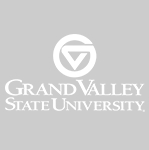
Magna Mirrors Engineering Co-op
Steven
Major: Product Design and Manufacturing Engineering
During my first coop at Magna Mirrors I had the pleasure to design two pieces of testing machinery, learn different techniques of finite element analysis and visit General Motors and Chrysler. I had opportunities to immerse myself in a variety of designs, prototype builds and in the field mirror testing.
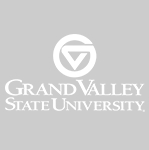
Vention Medical - 1st Term
Ryan
Major: Product Design and Manufacturing Engineering
I worked mostly investigating and dealing with customer quality complaints, such as assemblies and devices not meeting specifications. Problems were investigated by thoroughly testing each part of the devices. Testing often involved having to design new and unique measurement methods and fixtures. Once the cause of the problems were found, I would help come up with solutions and have them implemented as soon as possible.

Shape Corporation: Intern Experience
Chelsea
Major: Product Design and Manufacturing Engineering
Two main projects were assigned to me this semester. One project being an optimization project, where I developed a methodology to minimize mass on a grill housing unit. The part is normally full of ribs, and the program used told us what ribs are necessary. The mass on the part can be greatly reduced while still staying within the stress constraints, displacement constraints, and frequency constraints. I created a document that takes a user step by step through the process and did many presentations to engineers involved with the part as well. The other main project worked on was simulating the forming process of the ends of an aluminum beam. The ends are "crushed" to fit into the design space, but this process leads to high-stress areas. I set up the simulation and post-processed the results. A few smaller projects were worked on as well. Another optimization project to find a light weight high strength beam and several small tasks to help with the work the rest of the CAE team does.
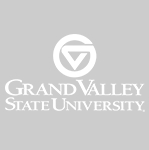
Blackmer Experience
Dustin
Major: Product Design and Manufacturing Engineering
Writing assembly instructions, complete with pictures, for 29 compressor models that Blackmer offers.

First Co-op at Autodie
Tyler
Major: Product Design and Manufacturing Engineering
I was part of the simulation department where I would take the developed parts from Catia CAD software and then placed it in Dynaform. In Dynaform I would mesh up the surfaced blank, post, cavity, and binders then checked for any issues like holes and other defects to the surface. I would setup the specific job and would run the simulation. After the simulation was done, I would open it in ETA Post where I would analyze and put together a report for Chrysler. I completed a project where all the active parts from the program would be simulated by dropping them on the nets described in the GD&T and using a new software we had just gotten. I had to create the net surfaces for each part then mesh them, set it up, simulate it, analysis it, and finally create a report for Chrysler and a PowerPoint for my coworkers on how to use the new software.

Engineering Co-Op 3
Kathryn
Major: Product Design and Manufacturing Engineering
I worked mostly with the manufacturing side of CHI implementing lean principles and new manufacturing techniques to their new line of Bliss chairs.
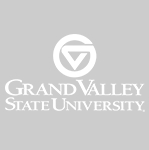
Hands-On and Fast-Moving
Stephen
Major: Product Design and Manufacturing Engineering
I ran production on multiple product lines that included stamping, laser cutting, injection molding, and assembly processes. I also led a team of six other interns in completing projects for the division that would improve machine efficiency or eliminate wasteful steps in weekly processes for the company. I completed projects dealing with machine or operator efficiency by implementing an automated pump system for lubricating oil for a reflector press and creating a standard component for multiple laser cutters that would save operator time when starting new coils of parts. I identified new projects for the team to complete, ordered replacement parts for machines, shipped products, and assisted in updating quality documentation.

Internship
Brittany
Major: Product Design and Manufacturing Engineering
I completed three red line packages. Red lines are the final model changes and job updates before a job is completed. I also was able to make a wire way cover and redesign a guide pin assembly that was creating an issue with its original design. I made templates for part changes on a current machine. I completed several detailing packages (prints), as well as, several detail checking. There was never a dull moment at work, nor was there a dull moment out of work! JR is a very community like company and provided me a great first co-op experience.
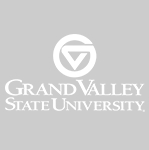
Projects: Long and Short
David
Major: Product Design and Manufacturing Engineering
As part of the main project I was placed with I was in charge of updating the Problem Solving Document, a Six Sigma tool used to analyze and keep track of projects. I ran tests on many solenoids, X-rayed them, and tore them apart to measure how certain parts had changed during calibration. I retrieved data from the End Of Line Tester and helped set up a work instruction for that task. One day some of the technicians called in sick and I helped keep the line running by fixing faults and supplying parts to the feeder bins.
One of the product lines was going to get a new machine in the assembly, and while I was being built I was asked to help feed parts through to make certain it was running properly.
I got some design work done with Solid Works. For one project I designed a gauge that would be used to measure terminal height at three critical points on the part. Another design was for parts that would help parts be picked up properly off of the track running through the annealing oven.
I was also tasked with acquiring a piece of equipment for the quality lab that would function like an Instron, but be easier to use.

Great Working Place and People
Nizar
Major: Product Design and Manufacturing Engineering
I have worked on different projects such as investigation engineering problems, testing new products, designing customized parts and equipment, making engineering drawings, modifying solid works models by design tables, and working on SAP system for engineering changes.
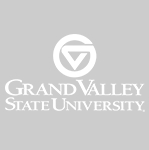
First Co-op Semester at Herman Miller
Daniel
Major: Product Design and Manufacturing Engineering
A primary focus of my internship was to evaluate potential uses for 3D printing within both my specific department and the company in general. I also designed a fixture which causes a sign to flip 180 degrees when a rope is pulled and completed several other smaller projects.
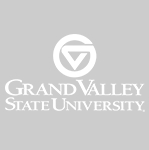
Vention Medical
Ryan
Major: Product Design and Manufacturing Engineering
I worked a lot on creating/updating a lot of maintenance and operating procedures for laser welding equipment. I also got to work directly with customers and suppliers in trying to solve product and process issues.
All opinions, conclusions or recommendations expressed are those of the author(s) and do not necessarily reflect the views of GVSU.