Experience Matters
You can filter your search by typing in an employer name, or selecting a major. This is a great way to see what possibilities are out there!

1st Co-op rotation at Gill Industries
Leif
Major: Product Design and Manufacturing Engineering
As a first rotation co-op at Gill, I had several different opportunities and responsibilities. With how Gill outlines their co-op experience, the first rotation is focused on exposing students to several different departments in order to understand every step of the manufacturing process from design to finished good. I began my semester working as a machine operator. Additionally, I developed operator work instructions and startup/shutdown instructions and posted them on new machines. In the manufacturing engineering department, I completed time studies on existing lines and came up with ways to improve efficiency and minimize unscheduled downtime.

Innovation
Connor
Major: Product Design and Manufacturing Engineering
I helped develop a specification for a powerfold for a company.

Engineering Co-Op
Jackson
Major: Product Design and Manufacturing Engineering
I wrote software for industrial applications using Python, Visual Basic, and HTML. I also performed mechanical design, circuit analysis, and statistical process control among numerous other things.

Engineering Co-op at Gill Industries
Jack
Major: Product Design and Manufacturing Engineering
During my second term as an engineering co-op at Gill Industries, I continued to gain a wide variety of skills and exposure. I rotated through four week intervals in product engineering, manufacturing engineering, quality engineering, and program management. I was able to design and manufacture prototypes for test fixtures, benchmark competitive products, develop an error detection system on an assembly line, learn how to run machines, and help with quality control. I was even able to collaborate with the other co-ops on small projects.

Emerald Corporation 2nd rotation
Peter
Major: Product Design and Manufacturing Engineering
Some of the job requirements that I have include equipment implementation, CAD modifications, data measurement analysis, project development, time studies, capability studies, writing work instructions, and project management of engineering changes. I felt as though I was able to get a wide range of different projects working in different areas of the manufacturing plant. I really got the feel for what Emerald does and what they are capable of doing. One part of my job that I enjoyed the most was getting to do some project management. I was able to manage engineering changes that occurred with current product. This involves; running my own weekly meeting, organizing Engineering change controlled document, and making sure the necessary jobs are done in a timely manner by the team.
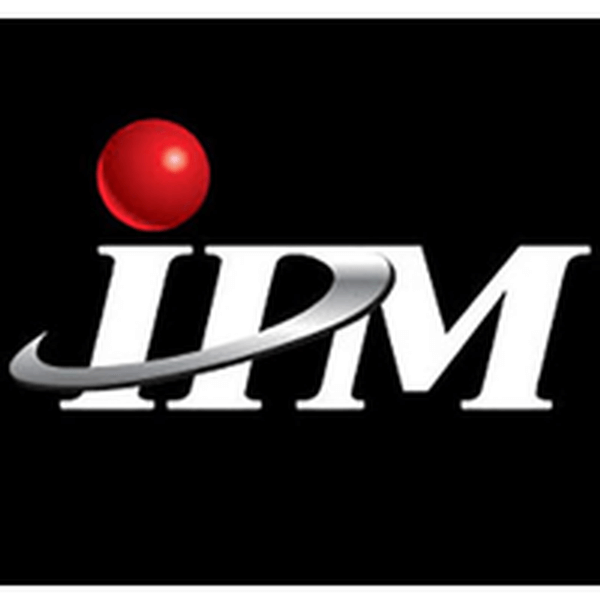
IPM Co-Op II - Beyond The Machine
Gavin
Major: Product Design and Manufacturing Engineering
This semesters experience was largely focused on a standardization project for several of our different conveyor product lines. The goals of this standardization project was to ultimately reduce delivery time from receipt of order to commissioning of a line. This required thinking outside of my traditional machine design roll, and focus more on processes and procedure than I would during a typical design process. During the course of this project, I spent a lot of time working with individuals throughout the company in a different capacity than I typically would throughout the course of a project. Aside from completing new equipment designs, I also worked with purchasing agents to develop new ordering strategies, mechanical builders on how to more efficiently deliver the information they need, as well as better equip our sales groups to accurately cost our equipment. I also worked to develop new process documents, libraries and templates, and finally trained my fellow engineers about how to best utilize the program. Once all of these deliverables were met, I helped apply the program to several customers' packaging lines and helped to realize the completion of customer's projects.
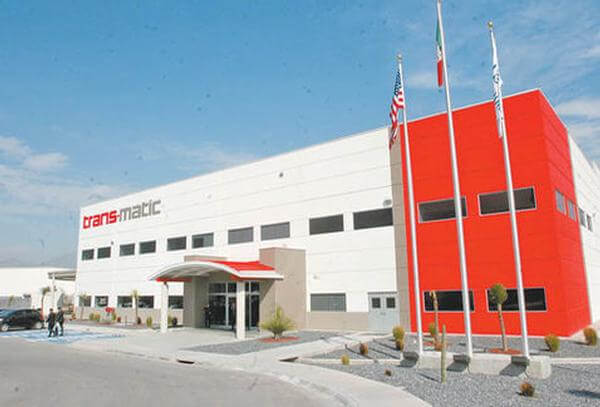
Interning at Trans-Matic Co-op II
Michael
Major: Product Design and Manufacturing Engineering
My second rotation at Trans-Matic involved: updating 3D cad prints using the Pro-E software, creating drawer layouts for organization of parts, and analyzing functionality of the company for continuous improvement.
Rotations at Trans-Matic have you explore different aspects of the company. Thus no rotation is exactly the same experience.
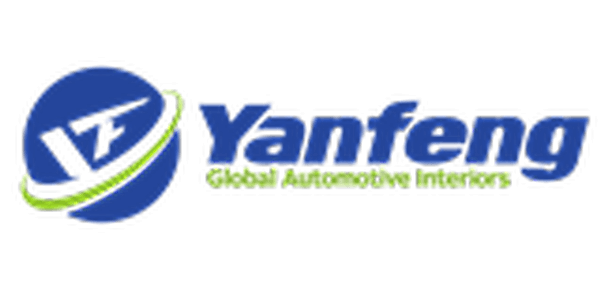
Second Co-op rotation
Ryan
Major: Product Design and Manufacturing Engineering
During this second co-op rotation at Yanfeng, I worked in the advanced manufacturing engineering department. Here I helped in launching a new product. In doing this, I participated in many conference calls, meetings with suppliers, and troubleshooting at the factory were the part is made.
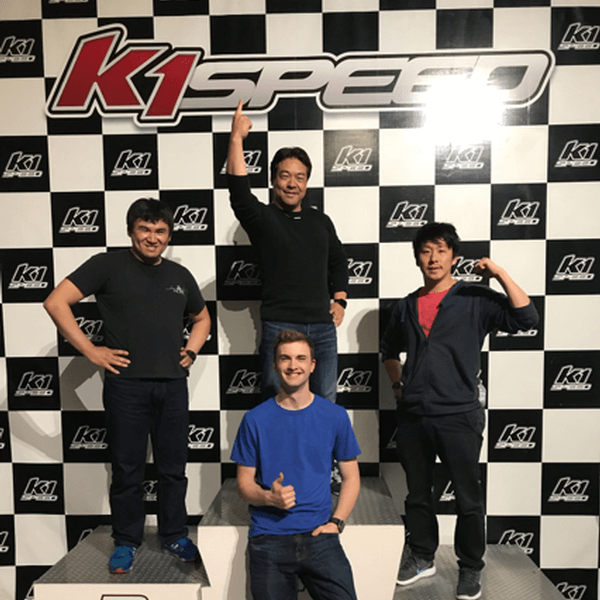
Co-op
Tyler
Major: Product Design and Manufacturing Engineering
I was responsible for supporting and performing tests on Pro Pilot Assist (our semi-autonomous system) vehicles. I identified leading competitive vehicles
which we used to evaluate the Pro Pilot Park feature. I attended the evaluation, performed some tests independently, and supported on others. I designed and performed a study to determine the appropriateness of the Pro-Pilot traffic jam timeout threshold. I also attended tuning for the new 2019 Altima. I assisted throughout the term with proposals, test route development, and instrumenting vehicles with test equipment.

Herman Miller Coop 3
Sean
Major: Product Design and Manufacturing Engineering
This semester I was given much more responsibility. I was taking on projects where I was the main engineer from start to finish. Some of these included figuring out the problem, designing the drawings needed, writing the program, purchasing the parts, and overseeing the install of the machine.

Yanfeng Co-op 3
Morgan
Major: Product Design and Manufacturing Engineering
Various tasks for the product engineering team on the launch of a BMW center console. Projects mostly related to part design changes, root cause analysis for quality issues, fulfilling testing requirements, and updating technical drawings. In this rotation, I traveled to two YFAI facilities out of state to support production work there and had a level of responsibility equal to a full-time hired engineer.

Project Engineering -Plastic Injection Molding
Dylan
Major: Product Design and Manufacturing Engineering
My third coop was focused on project engineering. This job was exciting and I learned a lot of valuable skills related to polymer processing and program management. I worked with other engineers on two main projects and was given a lot of independence with tasks. Each day was different and dependent on the task at hand and customer demands.
Read More About Project Engineering -Plastic Injection Molding

Innotec Co-op
brad
Major: Product Design and Manufacturing Engineering
During this last semester at Innotec, my time was split between my cell responsibilities (around 10 hours a week), production time (around 12 hours a week), and project time. My cell responsibilities were shipping, checking in materials, and safety. For shipping I would gather the parts that our customer had ordered for the day via a Hi-Lo. For material ordering, I would check in materials generally twice a week. We receive weekly shipments on most of our materials. The materials we use consist of large steel flat stock reels of 3 different size and thickness, copper flat stock reels, large barrels of 12 gauge and 10 gauge wire, and molded plastic housings. For safety, I would do monthly safety audits in our cell, complete at least 2 safety-related projects a month and inform other cell members of any safety concerns. The largest chunk of my time would go into projects. Most of my larger scale project were tied to Innotec's 8D system. With this system, you move the project through 8 steps: building the team, problem description, interim corrective action, root cause, permanent corrective action, validation, prevention and congratulations. I worked on mostly safety, MTBI (mean time between intervention), and changeover improvement projects.
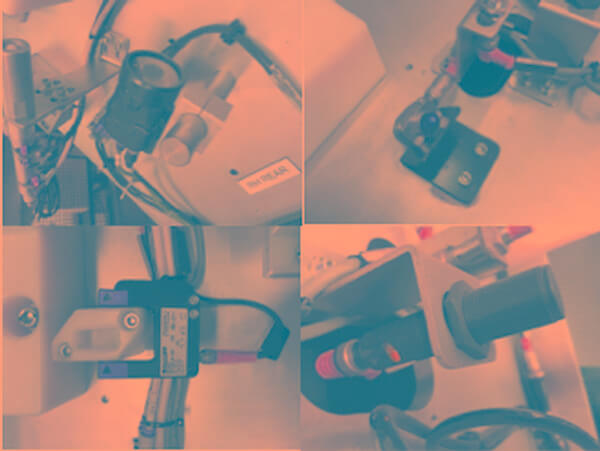
Southview Plant Engineering
Ryan
Major: Product Design and Manufacturing Engineering
During my summer co-op I worked in the assembly department at the Southview Plant. Much of my daily responsibilities revolved around what is known as continuous improvements.
I had daily HPT meetings which we would discuss possible improvements that could be made to the lines. I would then take these suggestions and work on implementing solutions. I did a lot of different projects over the summer for several different OEM lines.
I was involved in developing a screw shroud to be placed over a door panel before operators drive screws. The purpose of the shroud is to prevent dropped screws from becoming loosely stuck in the door panel during assembly.
I also helped create new verify matrix for the 2018 model year productions using a provided bill of materials. New features of the new model year required characters to be added to the matrix.
Another large project I worked on was creating job set-up doors for a particular lines. Job set-up doors are used at the beginning of each shift to verify that the array of visual, inductive, proximity, and contrast sensors are functioning properly.
I also lightly involved in other projects, such as the shutdown and removal of a line and a vinyl adhesion to substrate study using an Instron machine.

Gentex Co-op 1
Nate
Major: Product Design and Manufacturing Engineering
As part of the process engineering team in final assembly, the group I was working with was responsible for designing and building the machines for the production line of the full display mirror. The projects that I worked on included adapter brackets and mounts for displays, bar code scanners and totes. I also hand built conveyors, and flow racks and made design changes to those as they were being built. One of my main projects was a laser distance sensor for a machine that was strategically placed to detect whether a LCD was placed flat within the machine's fixture. Most of my projects required design work with CAD and hands-on work with the machine in the tool room.
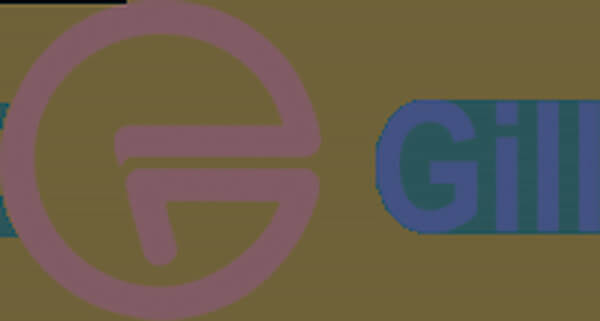
Engineering Co-op at Gill Industries
Jack
Major: Product Design and Manufacturing Engineering
The co-op program at Gill Industries involves 6 rotations through various departments. I began my employment operating a welding cell, then worked for the materials department, performing cycle checks and small inventory projects. Next, I was transferred to the press room, where I was not given any tasks/projects, but I observed the presses and stampings and helped my coworkers troubleshoot problems with the 1000 ton press. I then worked in the Quality Engineering department, in which I worked on multiple projects in Microsoft Excel and Plex, involving start-up checklists and quality checks. Finally, I worked with the Product Engineering department, performing various small and large projects, involving design, prototyping, testing and benchmarking. I will spend the last three weeks of co-op working in the Process Engineering department.
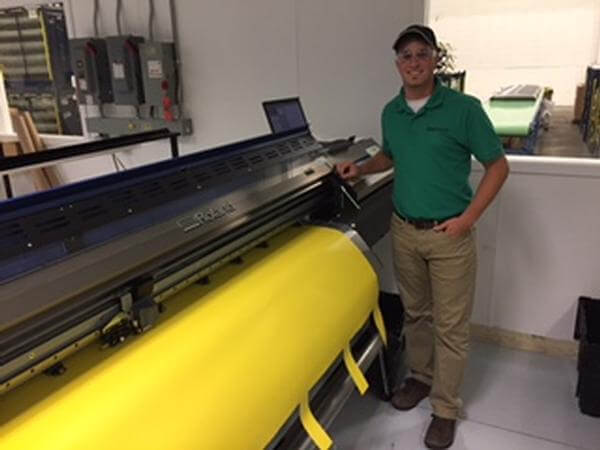
Manufacturing Engineering Co-op
Peter
Major: Product Design and Manufacturing Engineering
Some of the projects that I have accomplished include equipment implementation, CAD modifications, data measurement analysis, project development, time studies. I felt as though I was able to get a wide range of different projects working in different areas of the manufacturing plant. I really got the feel for what Emerald does and what they are capable of doing. One part of my job that I enjoyed the most was working with equipment (new or old) in project development. Often times when decorating a part, there is more than one way to do it. So determining the best way is crucial to meet quality standards and testing standards.
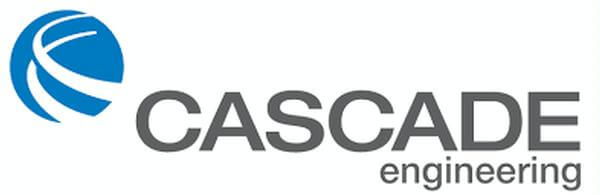
Cascade Engineering Co-op I
Landan
Major: Product Design and Manufacturing Engineering
Initially, I worked alongside production operators to learn the various products that Cascade manufactures and how the injection molding machines work. This allowed me to make relationships with the operators and support staff so I can be more effective when I am tasked on the factory floor. I also became very familiar with the products since I was constantly touching them and looking for defects which made me valuable to some of the engineers I would later work with since I knew their projects and how they were molded.
Later, I worked extensively on plastic dash mat prototypes with a Senior Engineering Technician producing the engineering changes required by the supplier and attaching the fiber to the plastic by sonic welding.
Also, I assisted in the testing of the waste containment carts and updating the master list for production date and material. Furthermore, I designed a stand that elevated the cart so that the wheels of the cart can be tested by the same testing machine.
Additionally, I conducted mold flow study using short shots from a press and a wall thickness study on a new dash mats that provided useful information to the engineers in their theoretical versus actual comparisons.
More, I pursued an independent project that was approved by my supervisor to improve a machine that I had worked on in my first weeks as a production operator. My improvements decluttered the factory floor and saved the operators time in clean up.
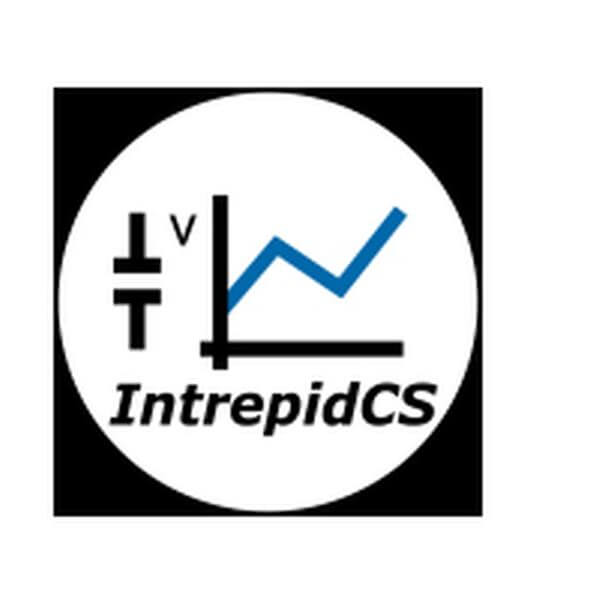
Intrepid CS (1st Rotation)
Drew
Major: Product Design and Manufacturing Engineering
At Intrepid I handled the design of the housing for these products. I also was involved with ordering parts for the products and seeking out quotes for materials and manufacturing jobs. Other tasks I was involved in were developing testing jigs for the our products and figuring out more effective ways to program more products at once. Also developing custom made ideas to make jobs for others easier for the production team here at the office.
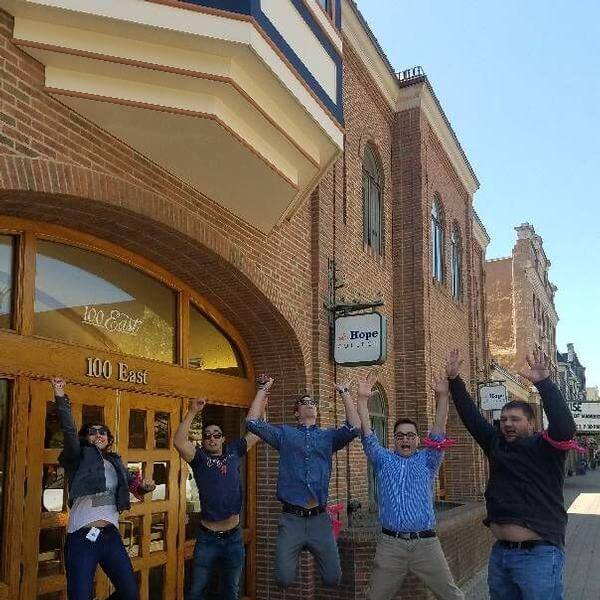
1st Semester Co-op: Gentex
Jensen
Major: Product Design and Manufacturing Engineering
I was tasked with designing, fabricating, wiring, and building a target thickness scanner to improve efficiency of cathodes used in the glass coating process. Measurements of the target cathodes were previously done by hand before installation and after their lifespan to measure erosion of the target (ruthenium/chrome). My design utilized a 3D scanning head running along a linear actuator that outputs dimensions and a 3D profile of the 9-foot cathodes. This will decrease the time for measurements and increase the accuracy.
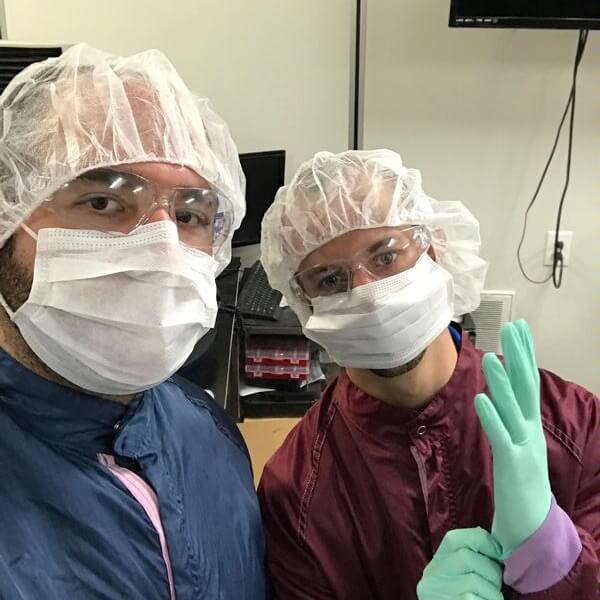
Design for Change
Connor
Major: Product Design and Manufacturing Engineering
During my experience at Magna I worked many prototypes that will eventually make it on cars. Being able to see the hard work on consumer product is a surreal experience. In addition, I was in charge of building display stands and benchmarking the competition.
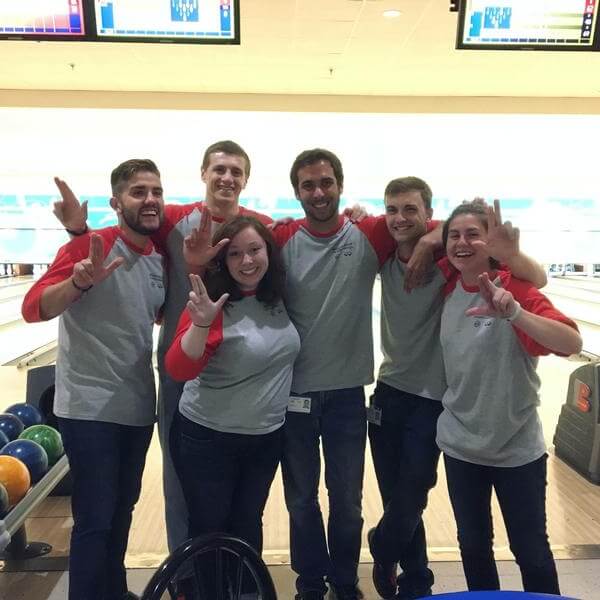
Engineering Co-op 1: TMG
Tyler
Major: Product Design and Manufacturing Engineering
I managed the testing of the 18 model year Nissan Frontier truck. This included monitoring test results from applicable groups, ensuring events were completed according to schedule, writing and releasing weekly reports to directors, sr. managers, and other applicable personnel, and in the case that a failure occurred, I would be responsible for tracking countermeasure development.
I was also assigned several additional projects which included tracking late orders from suppliers and presenting weekly status reports, building a vehicle quantity benchmarking database and developing vehicle quantity prediction formulas for future projects, revising/condensing/clarifying confidential vehicle camouflage guidelines, along with small tasks to assist my team when they were overloaded.

IPM Co-Op I
Gavin
Major: Product Design and Manufacturing Engineering
I have had previous experience with IPM outside of my first co-op, so I was able to hit the ground running with some new product development projects. As a Co-Op/Intern, you are expected to complete the full suite of task that any of the engineers would complete, including, but not limited, working with sales and project management to clearly define goals of the project, work with fellow engineers (both within your field of focus and not) to design a product or portion of an automated system utilizing Computer Aided Design, deliver manufactured components to mechanical assembly with the assistance of internal purchasing agents and local machine shops, a support the assembly and installation of designed equipment. Throughout the experience, the projects are "owned" by you, and you are responsible for every facet of the design, including attending important information gathering meetings, the ordering of components, and the support of testing and debugging equipment. However, your fellow engineers, as well as nearly the entire IPM staff are incredibly friendly and willing to help and answer any question you may have about the job function you are performing. Co-Op students complete work very independently, with knowledgeable and friendly people available to help facilitate learning in a team focused environment.
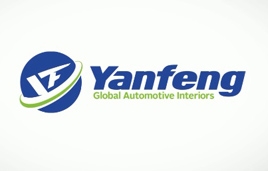
Yanfeng Automotive Interiors
Morgan
Major: Product Design and Manufacturing Engineering
This semester I worked in a plant as the manufacturing engineer on three door assembly lines. As part of that, I handled a wide range of tasks as they came up. This included working on the manufacturing line to gain experience, resolving safety and quality concerns, repairing machines as needed, leading a work re-balance to eliminate unnecessary production, and helping with on-going updates to equipment and processes.

2nd Co-op Rotation at Emerald Corporation
Trent
Major: Product Design and Manufacturing Engineering
During my second rotation of co-op at Emerald Corporation I was able to take charge and lead a few new projects. One of the projects was to come up with a new way to ensure traceability on all of the parts that are painted on our paint line. I was able to talk with many different printer and label suppliers to determine a plan of action to implement printers on our unload side of the line. These printers will allow Emerald to place labels on every part which will include important information about that specific paint run. If we have a quality alert from our customer we will be able to quickly determine a root cause based on the information printed on the label. Along with the leadership roles I was still able to enhance my CAD skills by designing new fixtures and even making edits to our plant floor blueprint.
All opinions, conclusions or recommendations expressed are those of the author(s) and do not necessarily reflect the views of GVSU.