Experience Matters
You can filter your search by typing in an employer name, or selecting a major. This is a great way to see what possibilities are out there!

Summer Co-Op for GVSU School of Engineering
Robert
Major: Mechanical Engineering
As an intern my primary purpose was to handle sub-projects to keep the launch moving along. Due to my previous experience with the company and the division I was able to go into the co-op handling larger projects. Primarily I was assisting an engineer who was handling the launch of two toolsets that would run production in another plant.

Summer co-op
Husam
Major: Mechanical Engineering
I worked on incoming inspection for prototypes and engineering changes. I also did corrective actions submissions for repeated quality issues, and worked on an 8D project.
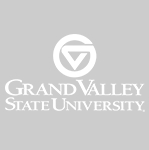
Manufacturing Engineer
Michael
Major: Mechanical Engineering
As a manufacturing engineer, I was responsible for designing, maintaining, and improving our facilities secondary operations equipment. Basically any operations that had to be done to parts after injection molding falls under a manufacturing engineers responsibility. I designed prototype equipment to cut blow molded tubes. I implemented a sensor to determine thickness of parts. I coordinated an engineering change to add labels to parts. And I learned the ins and outs of working with other vendors that design machines to perform operations that our parts required.
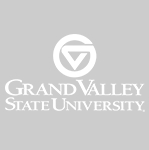
Brian's Haworth Internship
Brian
Major: Mechanical Engineering
While I worked in the wood plant with manufacturing engineers, I learned how to make organizational decisions related to a manufacturing plant.
In seating product engineering, I participated in cost reduction projects and quality improvements.
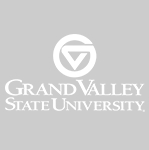
AUTODIE Internship
Luke
Major: Mechanical Engineering
I helped to make the company more efficient and productive by trying to eliminate wasteful activities. I standardized the concentration of coolant in the large Okuma CNC machines and in the cutoff saws and grinders. I compared the white light scans of the castings to the designs sent to the pattern shop to determine if we were adding to much casting to the parts that needed to be machined which would eliminate the amount and save money. I analyzed the data from the machines of all the times they weren't working on a job in order to find the most wasteful activities and tried to reduce the amount of time not cutting a job.

Engineering Co-op
Jack
Major: Mechanical Engineering
I was in the cost and concept development department. This is also called quoting or applications engineering. I quoted various machines for companies were looking for a machine or system to fit their needs. This meant if a company need a part assembled, test, or moved that they would tell JR the specifications and request a quote. I created the concepts and the basic layout of the machine they required and would put a price to it. This involved working with teams of design, build, and controls engineers.
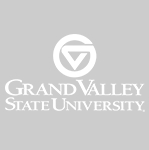
Engineer Intern
Austin
Major: Mechanical Engineering
Most of the projects I've taken on this semester have been ones that I can handle rather comfortably. Some have them have been a little more intricate though, like designing parts that will go into a job. I still know I can ask experienced engineers that will gladly help me with whatever I'm working on. The engineers at the place I worked know it will take time to get accustomed to the work that they do. Even when I get urgent jobs, they will still help me like time isn't a concern.

RDI Experience
Eric
Major: Mechanical Engineering
There were many projects and responsibilities that I had contributed to during the Engineering Co-op semester. One of the first projects that I worked on was to reverse engineer a simple ninja star gauge that was used to measure the tolerance of castings. Creo Parametric was used for all CAD modeling work. I gained experience placing the casting models on the parting line skins as well as creating the gating, casting vents, super vents, fire sticks, and crash pins. I did not work much with the design of risers, but I did however learn to manipulate existing risers to accommodate different casting models.
Sample travelers needed to be checked daily and I was assigned to do so. Each day I was responsible for checking to see if there were any samples that scheduled to run the following day.. The sample traveler indicates what properties need to be examined during a sample run including; shrink analysis, microstructure, magnetic particle inspection, and capability.
I also underwent fork-lift training which allowed me to put away high volume patterns once cleaned with an air compressor. I was responsible for checking if there were any breaks or cracks on each tool that was used.
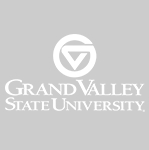
First Co-op
Matthew
Major: Mechanical Engineering
Calculate the tools, methods, timing to form the design concept. Researching and contacting other suppliers to gather costs of each part and process, to provide an estimate for the customer.

Project Engineer Co-op
Collin
Major: Mechanical Engineering
I was assigned to help with installing a double cone tumbler to mix all the pellets for one order but that came off different extruders so they might be slightly different colors. Tumbling the batched together assures a homogeneous mix. The tasks for installing the tumbler included planning how to load the tumbler and clean it as well as helping with testing and any problems we encountered. It was decided to load the tumbler by using a vacuum to create a low-pressure system inside the tumbler. The cleaning was done by water as well as air to dry it. I was to help with hooking up all these lines and designing the manifold which controls all these lines. I also helped pull wire for the tumbler and created drawings for the electrical schematics.
I was also tasked with a project to redesign a Rotex pellet sifter to fit a different machine. This was done by shortening the stand and ordering v-casters to ride on angle iron to prevent the machine from moving while in use. I also had to find a new way to load the Rotex for the new machine. This was done by using a different hookup from Siftex to allow for quick connect and easy cleaning.
Another project I had was to create a stand for a vacuum loader to load pellets from one Gaylord to another. I did this by creating a simple stand on four wheels and drawing up a plate for the loader to fit on and then create a swivel chute to easily maneuver between barrels being loaded.
With these projects, I was also assigned to help with most 3D drawings for the other projects going on in the process engineering department and parts ordering for these projects. I also helped update electrical, plumbing, and plant layout drawings for the whole plant as things changed. I was also sent to the Mexico plant for a week to update all the electrical and plant layout drawings after a new water system was put in place.

Flexco - 1st Rotation
Daniel
Major: Mechanical Engineering
My main project this summer dealt with creating quality control documents that will be used throughout the company to decrease the possibility of non-conforming parts making their way to the customer. I also worked on creating and implementing a capability study on Flexco's plasma cutter. Both of these projects involved working in cross-functional teams with almost every department within Flexco.
Additionally I helped resolve day to day quality issues as they arose and created work instruction documents that are used to train employees to do processes they had not previously done.

Quality Engineering in Sheet Metal
Kyle
Major: Mechanical Engineering
I worked in the quality department. On a day to day basis I aided in the high-detail inspection of products going through the shop. But all the time I was there I also had a major project going on in the background. I started off working on measuring and quantifying defective rates on DeWys' most difficult products, throughout production. This allowed me to gain in-depth insight into the processes and gain a significant knowledge about working with sheet metal. Then I took on a job researching new ways for our paint-line to mask their products. I was able to work with the upper management and eventually present my findings and recommendations to the leadership. Finally I researched lighting solutions in the shop. I worked with vendors, team leaders, and our management to present a final recommendation on what type of system should be installed.

Personal & Professional Growth
Jonathan
Major: Mechanical Engineering
My role in the organization for the last four (4) months can be defined as concept and cost development. I provided customers with solution concepts in the form of a quote. This document provides a system description, concept (3D model), and detailed cost breakdown.
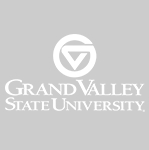
Engineering Co-Op - Innotec Corporation
Matthew
Major: Mechanical Engineering
The majority of my tasks focused on production of parts. I spent and average of 35 hours plus per week being responsible for production. This entailed everything from organizing incoming materials, organizing outgoing materials, filling materials needed for production, taking out scrap from production, cleaning up production areas, doing change overs between production models, fixing issues with production, and all other aspects of making products.
The remainder of my time was spent in meetings, ordering spare parts for my group, tracking internal scrap and rework parts, and preparing for the monthly divisional competition.
The amount of time spent on engineering tasks was negligible.
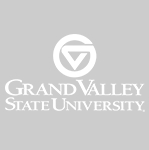
2nd Co-Op Semester
Robert
Major: Mechanical Engineering
I assisted with the launch of a laser cutting machine that was design to cut steel pieces to size. I completed tasks relating to controls, programming, mechanical design and debug, and machine prove out for launch.
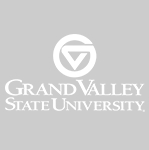
Innotec - Visors
Zachary
Major: Mechanical Engineering
While working in JVP covers, a cell which made visor covers, I completed projects, both large and small. I worked on a device that removed the pins from scrapped parts so that the remaining plastic part could be used as regrind in another cell's process. I also got experience working on controls in order to optimize the molding process, as well as streamlining the process.

Process Support Engineer
Derek
Major: Mechanical Engineering
Most of my semester was spent managing and supporting final assembly production lines. The tasks I performed required leadership, management of resources, and social and technical skills. When off the production floor, I worked on several continuous improvement projects and was able to implement them on the production lines during the time I was here.
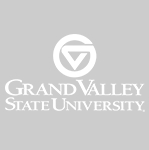
EGR 390 Co-op Experience
Matt
Major: Mechanical Engineering
Throughout the semester I worked closely with technicians and Engineers to help develop parts through the prototype phase of development.
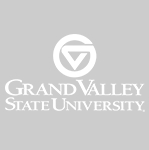
2nd Co/op at Autocam
Brandi
Major: Mechanical Engineering
I worked with the engineers on process improvements and quality issues.
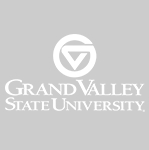
Environmental Engineering Internship
Nathan
Major: Mechanical Engineering
I have performed groundwater modeling using computer programs such as Visual MODFLOW, Surfer 10, ArcMap, and EVAP.
I have completed evaluations using the MDEQ's online Water Withdrawal Assessment Tool (WWAT).
I also have conducted multiple wastewater treatment projects, and performed groundwater and surface water sampling.
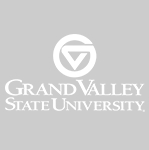
Gentex Co-Op Round 2
Andrew
Major: Mechanical Engineering
I worked in the glass bending department, the beginning of the process to complete an exterior electrochromic mirror. The vast majority of the manufacturing line components are designed by engineers at Gentex, and that lends itself to a lot of flexibility for future design improvements. I was given several projects to redesign a current component in the process, or design a completely new fixture in the case of additional safety or process count checks. I was also able to complete a previously started project of doing a tool redesign in the device that we use to level our glass bending process. I was able to update the design and technology used to take what was once a 4 hour process to one nearly half as long.

Part of the team
Evan
Major: Mechanical Engineering
Ran production, designed tooling and new additions to the machine line.

Second Co-Op At Innotec
Matthew
Major: Mechanical Engineering
The majority of my time was spent being production responsible. This entitled startup, shutdown, correcting machine stoppages, correcting machine errors, assisting manual process personnel, assembling boxes, cleaning the area, filling materials for production, reworking in process production parts, IMM tool changes, IMM cover changes, quality checks, and a whole other number of day to day issues.
When not being production responsible my two other main tasks were to monitor internal scrap / rework and spare parts levels. The scrap / rework responsibilities included formulating reports for the daily, three day, weekly, and monthly numbers, doing all rework for product that was unable to pass manual inspection, and alerting team members of any spikes or changes in internal scrap / rework.
The spare parts responsibilities was very straight forward. I was responsible for reordering any spare parts used in the day to day operations of the production area. I was also responsible for researching any parts needed for projects being done by fellow area members. I was responsible for getting the best price possible and keeping needed parts on hand. I would have also like to re-organize and set up a tracking system for the spare part storage areas, but this was not possible due to the large amount of production and other responsibilities.
The remainder of my time was spent fixing daily problems that occurred with production machines. I worked on a number of items through out the course of the semester:
- Bezel IMM Feeder
- Housing IMM Feeder
- Housing Circuit Pick And Place
- Housing Part Feeder Bowl Improvements
- Housing LED Install Improvements
- Bezel Feeder
- Bezel Finished Product Tote Stacker
- Reflector Scrap Track
- Circuit Die
- Making new production and area announcement boards
All of these "projects" were small items that were only addressed when production was stopped or interrupted as a result of that particular station being broken or malfunctioning. Some other small improvements dealt with wiring and fixing transfer problems. Overall, production was far more important and took priority over everything else.

GVSU 3rd and Final Co-op W15' Semester
Cody
Major: Mechanical Engineering
During the current semester I completed tasks related to advanced product development and product engineering. At Magna Mirrors in Holland I work mainly with the Inside Mirrors Division. I was involved with some design work and prototyping for the development of new products. I would often be asked to make prototype mirrors either for testing or customer samples. I was also involved with Root Cause Analysis for determining the root causes of problems with specific products. There were some projects that required designing fixtures or components using SolidWorks software, that would aid in the testing, development and manufacturing of products. I often would work with engineering staff to maintain programs: DFMEA's, DVP's, BOM's, benchmarking, design review checklist, tolerance stacks, drawing GD&T, DFM/DFA checklists and any other specified requirements.

Trans-Matic Engineering
Benjamin
Major: Mechanical Engineering
I was tasked with making sure the tooling drawings were up to date. I also spent half the semester on gage design. Gages are used to make sure the incredibly intricate parts are accurate to within 1/1000 of an inch.
All opinions, conclusions or recommendations expressed are those of the author(s) and do not necessarily reflect the views of GVSU.