Experience Matters
You can filter your search by typing in an employer name, or selecting a major. This is a great way to see what possibilities are out there!
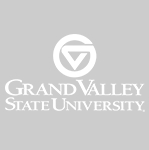
Costs and Concepts
Reuben
Major: Product Design and Manufacturing Engineering
I worked to develop concepts and quotes for customers on behalf of JR Automation.
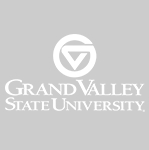
Manufacturing at Haworth
Kevin
Major: Product Design and Manufacturing Engineering
I was assigned as a manufacturing engineering co-op student. My tasks varied from cost-savings projects to plant layout redesigns. I also assisted some of the other engineers with daily tasks. One of the best opportunities that I was able to take advantage of was a kaizen. During these kaizens the company takes a problem and assigns a group of people closely related to the problem to solve it. These normally last a week long and end with thorough plans to fix the problem assigned.

Co-op 1
James
Major: Product Design and Manufacturing Engineering
During my experience I was given many different tasks. However, the majority of my time was spent learning the system and how to navigate and use their standards by updating part prints. A toolmaker would submit a change to a tool by designating it on the part print, and I would make that necessary change. Also, they would do the same for an entire book, and I would go through the book and update every part that needed it. I also designed many small projects including an automation project, and a threaded rod and its corresponding nut.
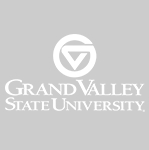
Putting Two and Two Together
Hayden
Major: Product Design and Manufacturing Engineering
The project I was given for the semester was awesome. The bezel on the 2013 Ford Escape's shifter slightly vibrates while driving. Right now, felt tape is being applied to these bezels before they are introduced into production. This tape is applied at a separate satellite station located a short distance away from the work cell. My project was to work this separate station into the cell, without slowing down their timing our their output numbers.
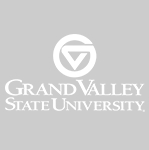
Engineering Co-op Earned Experience
Robert
Major: Product Design and Manufacturing Engineering
I was tasked with assisting engineers in the GM group with specific studies, testing and designing of program parts.
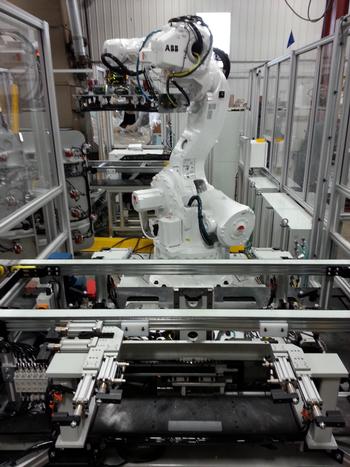
So, You Think You Learn a Lot in School? Try Working at JR Automation.
Eric
Major: Product Design and Manufacturing Engineering
While at JR I was privileged to be able to work on numerous different projects, all of which were unique and rich with learning experiences. I began my first weeks by learning my way around wiring and pneumatic diagrams, which are crucial pieces of documentation for every project the company becomes involved with. Once I became familiar with these, I was quickly given the opportunity to start learning the process of generating logic and debugging logic for PLCs using Rockwell's RSLogix5000. During this time I also learned how to use Rockwell's FactoryTalk View, which is a program that helps generate interactive interfaces that are unique for each project. This program downloads the interfaces onto HMIs (human machine interfaces), allowing users to view pertinent information, and even manually control actuation within the project.
I was able to put this information to use on several different projects, the most memorable being two different sunroof automation lines. For these automation lines I was given the task to help generate intuitive HMI screens for each station within the line. Since these were such large operations, there were as many as 30 different stations that needed unique displays. For each display that was created, logic also needed to be generated for everything to function harmoniously. While working on these projects, I was able to spend a good amount of time out on the floor, where I was able to go online with the PLCs that controlled the entire line, allowing me to make changes simultaneously with other engineers working on the project.
Read More About So, You Think You Learn a Lot in School? Try Working at JR Automation.
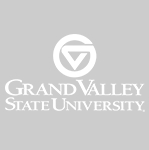
Experiences at Herman Miller
Andrew
Major: Product Design and Manufacturing Engineering
The options department is in charge of customizing products for special orders. I did a lot of CAD work and later learned how to process simple orders.
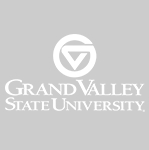
First Co-op at Autocam
Leah
Major: Product Design and Manufacturing Engineering
I have written work instructions, helped run machines/ maintain machines (washers, CNC, Screw machines), updated tooling documentations, performed quality vision reports, order/ design demag tables, etc..
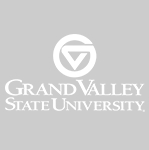
Developing A Company For Success
Joshua
Major: Product Design and Manufacturing Engineering
Developed a technical documentation format for the manufacturing facility and am training employees in technical writing and documentation for procedures within the manufacturing facility. Performing maintenance and continual improvements on the operator task entry computer system I designed and created in previous semesters. Created a new timekeeping system to replace faulty previous system. Developed a new much more robust inventory tracking computer system for the manufacturing facility that will began implementation within the next couple weeks. Performed R and D experiments for testing of the company product to allow for certification of further building standards for the product. Collaborated on Six Sigma Project with Plant Manager to assess motor power consumption of our manufacturing machines.
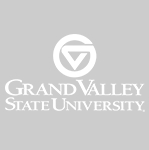
Practical Experience
Reuben
Major: Product Design and Manufacturing Engineering
During my Co-op, I was able to design several machines and machine components. I was also able to work on the shop floor and actually build/assemble one of the machines that I designed.
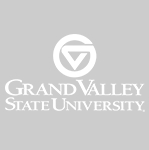
Great Experience
Alex
Major: Product Design and Manufacturing Engineering
Performed tests on current, competitor and prototype products to determine performance and analyzed the data to allow the engineering team to make informed decisions about what changes need to be made to make a product line better. Designed a self close and a push to open plastic module to fit inside the drawer slides that will one day be part of the KV product lineup.
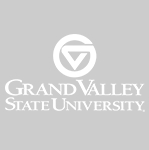
PDM co-op at Knape & Vogt
Alexander
Major: Product Design and Manufacturing Engineering
I worked in the Product Engineering department on new product development and the improvement of current products. Daily tasks included 3D modeling of design ideas that turned into either making or ordering prototype components and any all new designs needed research and calculations to prove they could be effective or not. Those products would then have to be presented in a clear manner that explained their workings for other employee's to understand. Also completed testing of the prototypes as well as current production products to compare to competitor products with data analysis of testing done to present to other employee's and give recommendations on the best option to proceed.
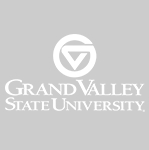
Options Engineer Co-op at Herman Miller
Andrew
Major: Product Design and Manufacturing Engineering
I was in the options department which is responsible for all the customized products. Specifically I work in wood cabinets which surprisingly are the most complex modified products.
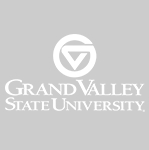
Irwin Seating: Co-op I
Heather
Major: Product Design and Manufacturing Engineering
My main tasks consisted of drawing and modeling work. I did a full overhaul of the material information on the drawings of plastic parts, helped other engineers with making dimensioned drawings, I made drawings of assembled chair options illustrating the important dimensions for architects and installers, modeled and helped design a prototype that would reduce tooling costs, and I also modeled and made dimensioned drawings for new reduced weight parts which were being developed. Along with this, I also did some work with the 3D printer. I printed objects for other engineers and designed and printed an aesthetic part for a prototype

1 of 3 rotations at Attwood Marine
Forrest
Major: Product Design and Manufacturing Engineering
I worked in the Quality Control lab, testing new products and old to ensure they meet up to standards largely created by the marine industry.
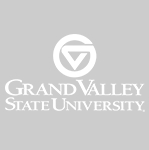
Herman Miller - Manufacturing Engineering Co-Op
Nicole
Major: Product Design and Manufacturing Engineering
I worked on a capacity study of their panel saws to determine how many parts could be produced every shift. This incorporated a variety of variables including different sized parts cut from a sheet of material, a different number of sheets cut at a single time, and varying ways to cut each sheet.
I helped with new shop floor layouts that would create space for new machines that were on order and re-arranging the current work cells to accommodate the new machines.
I also participated in a corporate Intern Project, which is different every year. This project that I worked on was evaluating the training of new hires in their Customer Service groups and providing recommendations to improve their training programs. These recommendations would allow them to have new hires prepared to assist customers faster and would help Herman Miller provide even more excellent customer service.
Some other projects I did this year included: ergonomic assessments, designing fixtures, and designing guards for their hanging staple guns. The ergonomic assessments evaluate the movements of workers on the shop floor and determine if something needs to be changed in the process to help them to have more ergonomically friendly movements.
Read More About Herman Miller - Manufacturing Engineering Co-Op

EGR 290 Co-op
Brian
Major: Product Design and Manufacturing Engineering
On a regular basis I will make machine parts, frames, and plates from stock metal. First cutting them, then squaring them up with a mill or CNC, then drilling them where needed. I will assemble the frames and make risers from them, cut and finish tubes, attach casters to them, as well as finished plates to create a table. The table is the base which the entire machine is built upon. Some of the less complex parts I will cut from stock and finish myself.
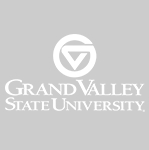
Co-Op at Koops
Michael
Major: Product Design and Manufacturing Engineering
At Koops, I interned in the controls department. This section of the company is concerned with programming the machines to perform the task desired. I worked on various projects that speed up manufacturing processes, programming the digital logic that commands the actions of the machine and the interface an operator uses to communicate with the machine. The controls team is able to help with design changes as the machine is dry run and debugged, as the project as designed often must receive further adjustments before it is shipped to the customer.
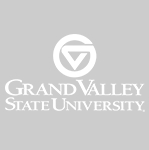
Engineering Customized Product at Herman Miller
Andrew
Major: Product Design and Manufacturing Engineering
I work in the options department on wood storage products. On top of this I investigated the use of a new 3d modeling software to see if it could be used to make our technical illustration creation process more efficient. And in this last semester I used my 3d modeling knowledge to help management solve some communication issues between the applications and engineering departments. It was good to see how management solves problems this semester.
Read More About Engineering Customized Product at Herman Miller
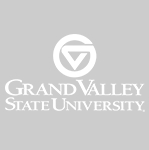
Manufacturing Engineering at Herman Miller
Nicole
Major: Product Design and Manufacturing Engineering
The main project that I completed this semester was a capacity study for a variety of machines. A capacity study determines how many products a machine is able to produce in a given period of time. This helps in high-level decision making such as when to add another manufacturing shift or when to purchase more machines.
I also worked on deciding if a proposed process improvement: to use a larger router bit to cut holes in the work surfaces, would be cost effective. I needed to compare the cost of the new bit to the cost of the smaller bit currently in production and also consider the benefit to Herman Miller that this change would provide.
The last major project that I worked on was to begin organizing a system to track certain machine parts as they were shipped out for repair and as they were moved throughout the manufacturing plant from one machine to another. This would help us to detect quality issues and ensure that repairs were made to these parts in a timely manner.
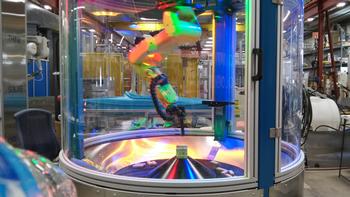
Learning and Growing at JR
Brittany
Major: Product Design and Manufacturing Engineering
I finalized drawings, bills of materials, master parts lists (MPLs) and also designed parts for builders as necessary. I learned a great deal about excel coding and as this was my second term in design I was able to practice and reinforce JR design processes and standards. As unexciting as excel coding sounds it was actually quite interesting and involved. I was actually able to automate the process of building a master parts list and was able to share that with our customer which felt great.
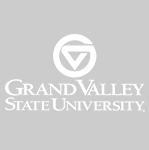
Engineering at Koops
Michael
Major: Product Design and Manufacturing Engineering
I worked as a launch engineer, verifying the mechanical and electrical designs of the machines. Confirming machine functionality and debugging design, controls, or electrical issues all played a role in my day to day tasks.
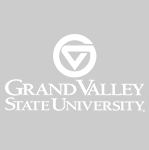
NASA Langley Research Center Internship
Amanda
Major: Product Design and Manufacturing Engineering
Over the course of my internship I worked in the Systems Integration and Test Branch (SITB). I worked with both technicians and engineers in day-to-day operations and both preparations and running of thermal vacuum tests. I was also given the opportunity to complete and present a project that took the full semester. During thermal testing contaminants are collected on cryogenic surfaces. This is included in the test because the hardware will be operating in space where there is high fluctuations in temperature depending on which side of Earth the equipment is on. When the equipment moves from the hot side to the cold side there is a possibility of a condensation-like film that can occur on the surfaces. The purpose of the cryogenic surface is to collect the partials that will cause the film and remove them from the hardware. It also allows for the particles to be evaluated to determine the degree of danger they possess to the hardware. My project was to write a procedure about how to evaluate the rinse from the cryogenic surface using Fourier Transform Infrared Spectroscopy.
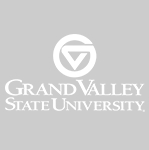
Manufacturing Engineering at Haworth
Kevin
Major: Product Design and Manufacturing Engineering
During my time at Haworth I worked in the laminated products plant where the worksurface, casegood products and some panel components are made. I was able to attend a couple of Kaizen events where a team was brought together to tackle a project within a relatively short period of time. During these events I was tasked with creating and developing CAD drawings of the plant layout and help with determining ways of overcoming problems and improving productivity.
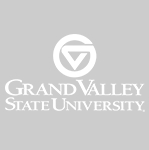
Lasting Impressions
Hayden
Major: Product Design and Manufacturing Engineering
This was my third and final rotation at GHSP. Over the course of the semester, I was tasked with different root cause analysis assignments. I helped record and track a major failure as well as work with the team designated to solve it. We made some major breakthroughs and I found a lot of valuable information from my data. I was also given the failures from our dyno tester to sort and analyze. I've helped look through and determine the causes of some of these varying failure methods we have seen.
All opinions, conclusions or recommendations expressed are those of the author(s) and do not necessarily reflect the views of GVSU.