Experience Matters
You can filter your search by typing in an employer name, or selecting a major. This is a great way to see what possibilities are out there!
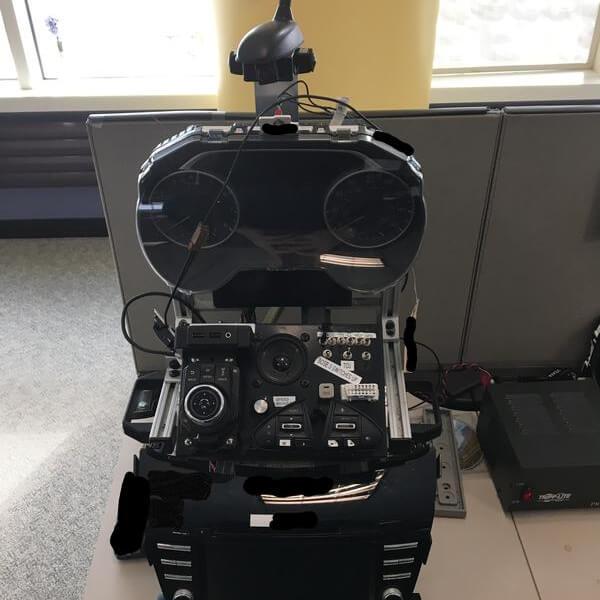
Audio/IT Test
John
Major: Electrical Engineering
My co-op focused in two areas: Test Bench Creation & Assisting in Vehicle Tests. Most of my time was spent designing and creating a test bench area that is meant to seamlessly simulate a vehicle's Audio/Infotainment functions (Meter, Head unit, navigation, USB Port, Radio, SXM, etc). By using the test bench, the engineers can perform all software tests without getting into an entire car. Thus saving time and the number of reserved vehicles for the department.
I collaborated with other engineers to design & build a mechanical frame to place all of the equipment. Then, documented/constructed all of the electrical wiring & harnesses that connects each device together to form a complete system.
On another note, each week I acted as an assistant for my co-workers in performing various vehicle tests such as GPS Synchronization, USB Performance, etc.
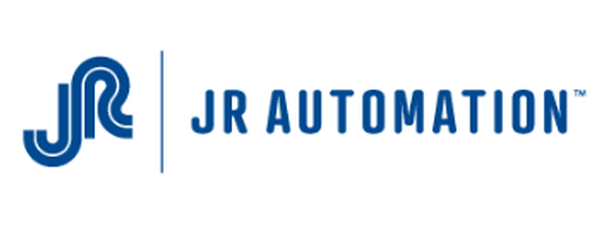
JR Automation Co-op 2
Natalie
Major: Electrical Engineering
I spent time this semester doing a few different things. The first thing I worked on was making red-line changes to electrical and pneumatic prints. Next, I set up a vision system to be able to take a picture of a completed part and determine whether is was good or bad. After that, I was placed on a project team and got the opportunity to assist in the PLC programming and creation of HMI screens for a new project. I also spent a little bit of time teaching points to robots.
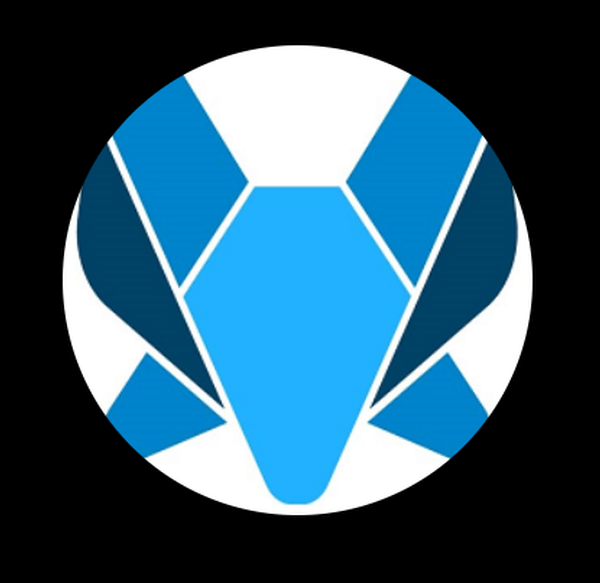
Co-Op I
Michael
Major: Electrical Engineering
Tasks include supporting the product manufacturing team with Work Instructions, updating Bill of Materials, and releasing Engineering Change Notices. Projects include creating Testing Fixtures that ensure all of our shipped products meet specification.
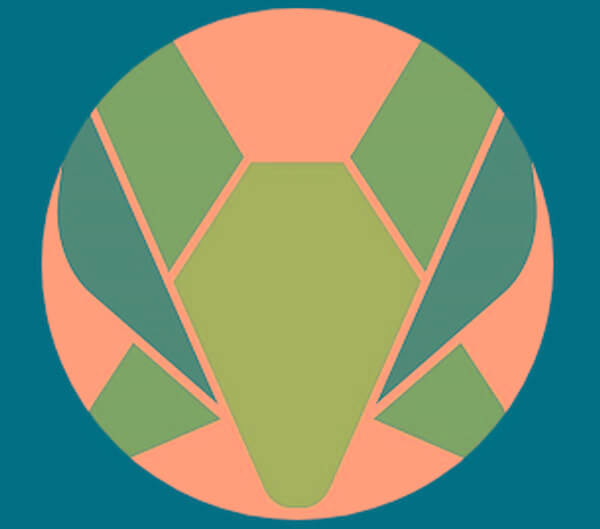
Electrical Engineering Third Rotation
Chris
Major: Electrical Engineering
During this semester I was able to work on multiple projects. I was assigned the task of designing and fabrication an end of line for our production line. This project involved a circuit layout, Linux and C coding, and mounting and fabrication of the enclosure. I was also able to design and work on multiple different products for out customers.
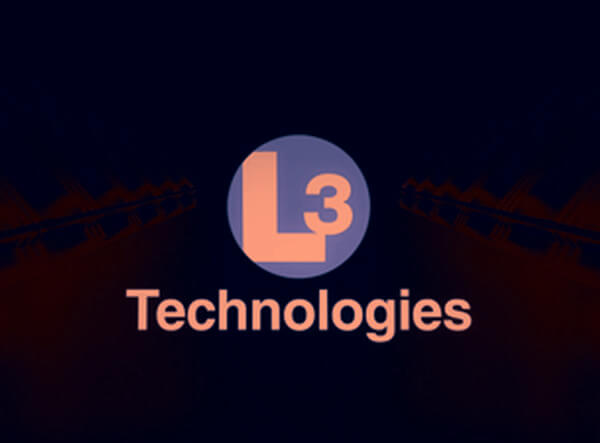
Co-op 3
Nicholas
Major: Electrical Engineering
I was part of the daily tasks that would help keep production running smoothly while also being part of the bigger projects associated with testing. I specifically was in charge of designing a brand new test station that was to be used in the testing of batteries before a product is shipped out. The process in creating such a station included both hardware elements and software elements that taught me a variety of skills.
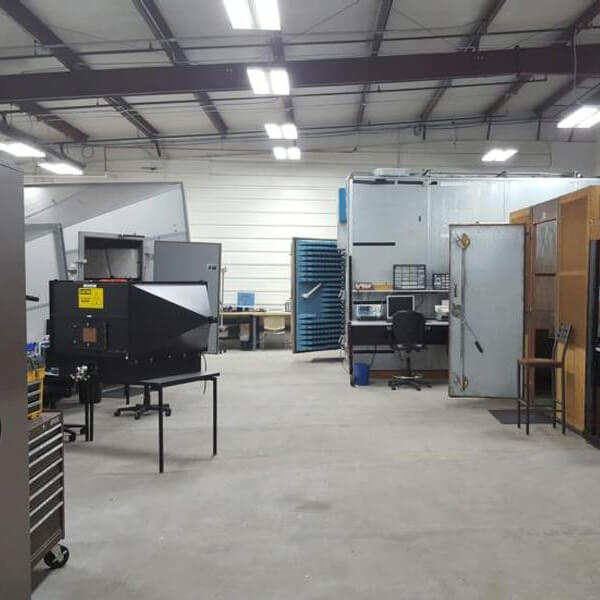
EMC Co-op Third Rotation
Daniel
Major: Electrical Engineering
During the third rotation of the co-op, I worked with clients to run a variety of test such as Radiated Emissions (RE), Conducted Emissions (CE), Bulk Current Injection (BCI), Radiated Immunity (RI), and Electrostatic Discharge (ESD). Compared to the prior rotations, I was a lot more independent working with client's to perform these tests. I also worked on the diagnostic aspect of the products to understand how the product circuitry was producing failures and how to reduce these failures (debugging).

Third Co-op Rotation
Matthew
Major: Electrical Engineering
This is my third and final co-op rotation at JR and it has definitely been the best one so far. I've had the opportunity to be very hands with the machines I've worked on. I've been able to design the electrical systems, program the machines, work with robots, design the operator touch screen layouts, troubleshoot wiring and pneumatic issues, attend meetings with the customers, and travel to the customers location for machine installation.

3rd co-op rotation
Nathan
Major: Electrical Engineering
My role included various PLC and HMI programming tasks, the control of varying frequency drives, servo motors, conveyors, and various other pneumatic/electrical jobs.
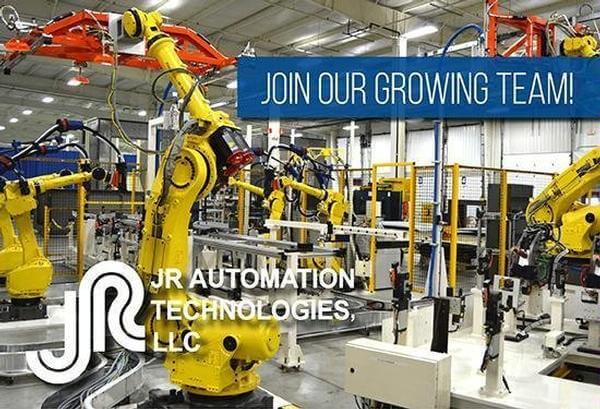
1st Co-Op at JR Automation
James
Major: Electrical Engineering
Over the course of my co-op rotation, I completed a good deal of programming in both HMI (Touchscreen) and PLC (Ladder Logic) formats. I also helped troubleshoot issues with electrical, pneumatic, and mechanical problems on various projects at my business unit.

Automation Design
Joseph
Major: Electrical Engineering
While working at Koops I got to experience first hand the design process of creating automation systems. Some of the projects I was assigned during my time at Koops was working side by side with other engineers to design automated systems. Another project I was assigned to was updating older automated machines. All of these task contained a great deal of engineering work such as design analysis, technical drawings, stress and strain analysis, and etc.
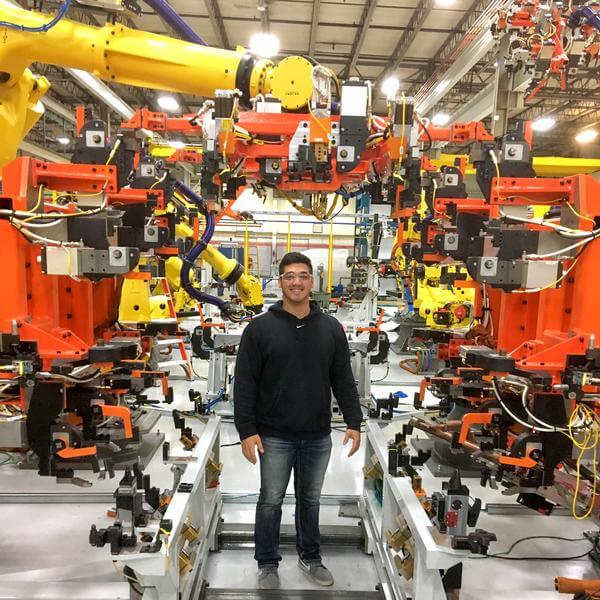
Controls Engineering in Automation
Kyler
Major: Electrical Engineering
After working with AutoMatrix for the summer I was able to design, wire, program, and troubleshoot various machines in the automotive industry. AutoMatrix focuses on automating processes that help other businesses improve efficiency and productivity. Although they are a smaller company, they take on some very large projects for very reputable companies. My co-op experience consisted of programming a machine that loaded magnets into a rear-view mirror holder for a new electric car company. I also designed and programmed a laser marking system for the same company. The machine was responsible for providing a VIN number and logo on both front and rear bumpers.

Twisthink Co-op Part 1
Christopher
Major: Electrical Engineering
During this semester I worked on vision system projects, test setups, Wi-Fi pattern testing, board modifications and component tests. Since Twisthink is a consulting firm, it gave me the opportunity to work on a variety of different projects for a variety of companies. For the vision system projects I ran tests with multiple camera captures and wrote a variety of MATLAB scripts to analyze the results and modify the images. This also involved a lot of data formatting and developing file structures. For the test setups I build and evaluated setups for Wi-Fi pattern testing and fluid water sensing. I also did a lot of Wi-Fi pattern testing to determine the best locations for Wi-Fi board and external antennas on appliances. This involved mass data collection, data analysis, board programming and board modifications. Over the course of the semester I assisted in the rebuilding and redesign of the test platform that we currently used for Wi-Fi testing. Finally I did a lot of board modifications that included working under the microscope to change resistors, rewiring board and making a variety of harnesses.

Testing ,Testing, 123
Tom
Major: Electrical Engineering
My work at L3 was focused on Test Engineering and the rigorous testing process which aviation products have to go through. Software work was emphasized as much of the mechanical/ electrical aspect of the design is taken care of by the initial engineering team as the products are designed. Work towards a "station test box, test" was the bulk of the work done during the co/op. This involved building intricate knowledge of the circuits and signals involved in the testing of a set of products as well as working with software to send and receive specific in order to check their validity.

Co-op Rotation 1
Collin
Major: Electrical Engineering
The work was very software focused with most hardware work being more basic, systems level analysis. I worked on creating new test engineering software packages as well as assisting in updates to existing software. However, the nature of what the software was being written for still necessitated an understanding of electrical engineering concepts.

Great Place to Grow
Logan
Major: Electrical Engineering
Quality control projects for production lines. Improvements in the production efficiency. Prototyping for off-road vehicle lighting.

Controls Engineering Co-op
Collin
Major: Electrical Engineering
My day to day activities included designing system layouts of control devices necessary to the operation of the system, drawing these systems in AutoCAD, and the documentation to support these installations. Once the system design and schematics are complete, the software has to be written for the programmable logic controller so it can correctly processes the input and output devices previously added.

Gateway to learning Electronics
Brad
Major: Electrical Engineering
The electronics lab was responsible for a large portion of the testing equipment used on the production floor. The most popular testing unit is known as the "lunch box" these are small boxes that allow the user to power a tail lamp and test the functionality of each lamp. Each of the boxes are built for a specific model of lamp, meaning that there are hundreds scattered around the plant. I was given the task to build these as well as maintain them when they broke. I also build more advanced testing units known as "smart lamps" these lamps allowed for individual LED control and were programmed with a micro controller. Throughout this rotation I specifically worked on the Ford Edge and the Ford Mustang.

Co-Op at Johnson Controls
Dan
Major: Electrical Engineering
I am responsible for process development. I completed electrical schematics for a conveyor oven and developed a laser weld for hermetic sealing of lithium ion cells.
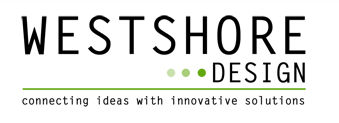
EGR 290
David
Major: Electrical Engineering
I was assigned a main project to work on throughout the co-op. This project had me design a peak current meter that was capable of measuring the peak on time current as well as continuous current of all types of industrial LED driver products. The meter was capable of measuring a wide range of current. I also worked on many smaller projects that allowed me to get experience with a variety of products.
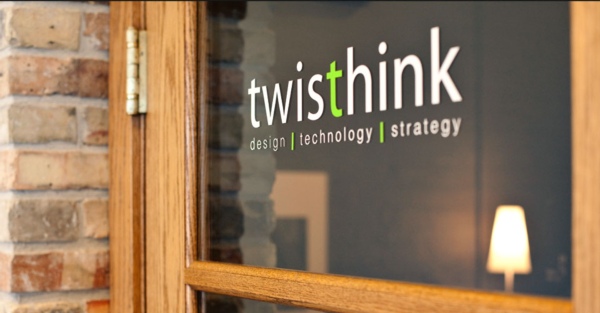
2nd Semester Co-op
Karla
Major: Electrical Engineering
Mainly, I worked on maintaining and writing tests for a Hardware in the loop test system. I also performed manual tests, tech work in the lab, and rf antenna testing.
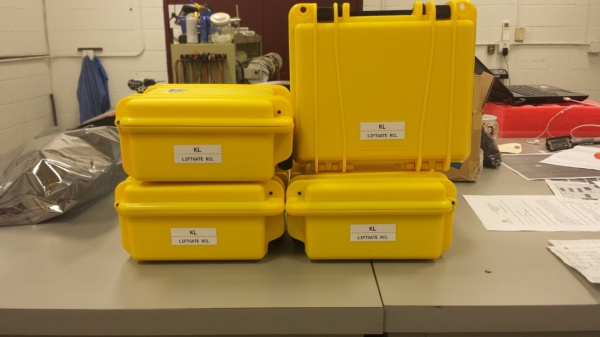
Co-op II
Joseph
Major: Electrical Engineering
I assisted in the plant electronics lab, doing what ever needed to be done at the given moment. I repaired and built mobile product test unit for our production floor and customers (shown in the experience submission picture). I performed ESD testing to help design a board layout change. I developed test masters for the end of the line test stations. I also conducted failure analysis of warranty returned parts as well as managed some maintenance improvements in the lab itself.

Gaining Automation Experience
Matthew
Major: Electrical Engineering
Throughout this second co-op rotation, I was tasked with many new responsibilities that I didn't get to do on my first rotation. These responsibilities included designing and implementing a Human Machine Interface (HMI), establishing communication to the machine's components via various communication protocols, setting up the machine's diagnostic settings, and programming the machine. I was also involved enough in a project to leave the plant and help out with the installation and debug process on the customer site.

EMC Co-op Second Rotation
Daniel
Major: Electrical Engineering
During the second rotation of the co-op, I worked with clients to run a variety of test such as Radiated Emissions (RE), Conducted Emissions (CE), Bulk Current Injection (BCI), Radiated Immunity (RI), and Electrostatic Discharge (ESD). Compared to the first rotation, I was a lot more independent working with client's to perform these tests. I also worked on the diagnostic aspect of the products to understand how the product circuitry was producing failures and how to reduce these failures.

JR Automation 2nd Rotation
Nathan
Major: Electrical Engineering
For the first few weeks, I was placed on a project to get a repeat job's fixture up and running given the PLC and HMI. This was a great refresher and got me back into the controls engineering mindset.
Next, I spent a little over a month on a much larger project with various tooling fixtures. This taught me a great deal about the hardware implementation of several devices, while building my PLC and HMI programming abilities.
Finally, for the last two months, I have been doing a lot of design work. This included designing electrical and pneumatic prints for various jobs. I learned an outstanding amount about the automation process, as well as electrical and pneumatic functionality.
All opinions, conclusions or recommendations expressed are those of the author(s) and do not necessarily reflect the views of GVSU.